Energy requirements for the operation of a
chiller account for a significant amount of total energy requirements. An
effective water management program is essential in controlling energy usage.
However, even the very best of water management programs do not totally
eliminate scaling. Minimum levels of even soft scale accumulation on
condenser tubes will greatly increase the annual energy expense. Today,
there is an innovative solution available that will improve chiller
performance by eliminating scale, translating into substantial energy
savings. |
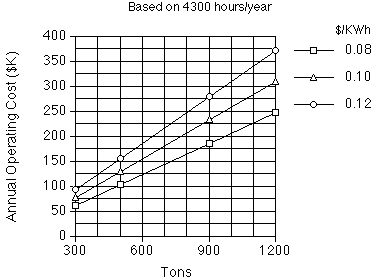 |
Fig. 1 Annual Operating Cost vs. size of chiller for three different
electric costs.
|
Wasted Energy Due to
Fouling
Energy consumption is dependent upon the
efficiency of a chiller, hours of operation, average load, cost of
electricity, and the amount of fouling. Figure 3 depicts the additional cost
incurred due to fouling. For example, when the fouling factor is 0.003 (i.e.
scale thickness of 0.036 in.), the additional energy cost per year for a 500
ton chiller is $25,300. Energy savings of equivalent amounts can be realized
with effective water treatment.
|
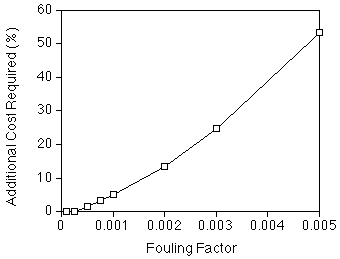 |
Fig. 2 Additional Energy Cost required due to Fouling in Condenser Tubes
|
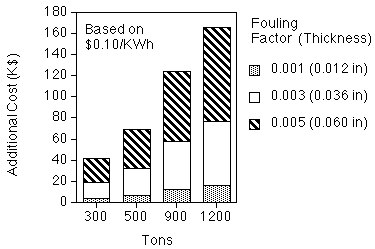 |
Fig. 3 Additional Cost Incurred Due to Fouling in Terms of Chiller Size
(tons). This data is based upon actual kilowatt per ton data as a function
of the fouling factor, and was provided by York International Applied
Systems. |
Traditional
Maintenance Techniques are not Enough
Condenser tubes last significantly longer if
properly maintained. Once fouling occurs in condenser tubes, scales are
removed by using acid, steel brushes and abrasive cutters, which shorten the
life of the tubes. Premature replacement of these tubes is expensive. An
investment in preventive maintenance such as the ED 2000 system can prevent
this additional cost.
|
The ED 2000 Solution
Electronic Descaling (ED) 2000 offers an innovative electronic solution
to significantly reduce scales in condenser tubes. The source of scaling
problems lies in recirculating water whose TDS (total dissolved solids)
level is often above 1500 mg/L. Even in a soft water region, the TDS level
of the recirculating water is high due to the evaporation of water in the
cooling tower. Because of the inverse solubility laws, dissolved mineral
ions such as calcium, bicarbonate, etc., precipitate as the water is
heated in the condenser tubes, resulting in the deposition of scales on
the tube walls. This phenomenon we call "uncontrolled
precipitation."
The ED 2000 solution, called "controlled precipitation"
causes the dissolved mineral ions to precipitate in the feed pipe of a
condenser, thus preventing mineral ions from adhering to the condenser
tube walls. Solenoid-induced molecular agitation (SIMA™), created by the
Faraday's law, forces dissolved mineral ions to precipitate to large
insoluble mineral crystals. By this "controlled precipitation"
the crystals suspend in the water and do not adhere to the condenser tube
walls. The precipitated particles settle at the bottom of the tower sump
and are removed through regular blowdowns, resulting in lowering the TDS
level of recirculating water and the consumption of water.
The presence of scale in condenser tubes decreases the efficiency of a
chiller, greatly increasing energy cost. Small amounts of scale, even with
effective treatment systems, may increase cost of operation by 30% or
more. By preventing even small amounts of scale build-up, the ED 2000
Anti-Fouling System provides enhanced performance and lower energy
consumption.
|
 |
Fig. 4 "Controlled precipitation" converts dissolved mineral
ions to insoluble crystals, thus preventing the new scale in condenser
tubes.
|
Field Test Data
(Atlanta, GA, data from York International)
|
|
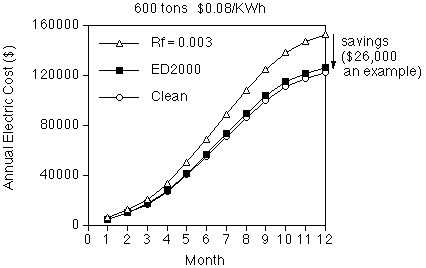 |
Fig. 5 Annual Electric Cost vs. Month of Operation. Due to the use of
ED2000 Anti-Fouling System, significant savings can be achieved.
|
Procedure to check
whether ED2000 Anti-Fouling System keeps condenser tubes fouling-free or
not
|
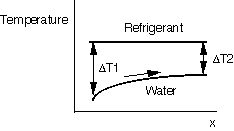 |
One can monitor the approach temperature, DT2,
defined as the temperature difference between refrigerant outlet and
cooling water outlet in condenser.
|
 |
Without Anti-Fouling Device, chiller performance as measured by the
approach temperature, DT2, will decrease with
time, requiring ever-increasing energy as the cooling season progresses.
With Anti-Fouling Device, chiller performance as monitored by the
approach temperature, DT2, remains at the
initial fouling-free capacity, and energy requirement is the same
throughout the year as the one in the beginning of the cooling season.
|
|
Effect of Fouling
Factor on Electric Energy Consumption |
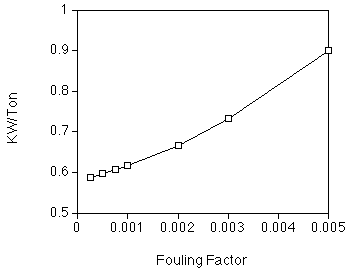
|
|
|
|
|