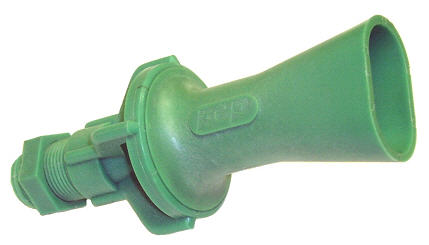
Sweeper Jet
Electric H2O's Sweeper
Jet is designed specifically for cooling tower basins. In order for
cooling tower filters to do an effective job removing solid
contaminants from the cooling tower basin, the solid particulates
must be directed toward the filter inlet. Our Sweeper Jet nozzles
achieve this through a uniquely designed elliptical discharge outlet
that directs basin water toward the filter inlet in a flat fan
pattern. This maximizes the performance of any cooling tower
filtration system by actively sending particulates and sedimentation
from stagnation zones in the tower sump to the filter. Dollar for
dollar, the Sweeper Jet is among the most effective ways to improve
water treatment performance.
Using the venturi
principle, Sweeper Jets create a negative pressure region at the
nozzle outlet, thereby forcing water into the elliptical discharge.
This permits the use of a smaller pump to deliver the volume of
water required for effective sweeping of solids to the filter inlet.
The elliptical pattern sweeps a large path width, achieving a
significant reduction in stagnant areas between nozzles. By
directing solids toward the filter system suction intake, the
Sweeper Jet system sharply reduces build-up of dirt, scale, airborne
debris, sediment and other contaminants in cooling tower basins,
sumps and machinery reservoirs.
Sweeper Jets are installed into a
pipe that runs along the cooling tower basin bottom. Clamp-on swivel
mounts are available to direct the sweeping path into hard-to-reach
areas and to accommodate irregular shaped basins. Electric H2O
provides sweeper jet systems tailored to each application. Basin
size and shape, liquid depth, competing flow characteristics, solids
loading and other site-specific criteria are examined for optimal
flow and cleaning results. From there, Electric H2O determines the
correct Sweeper Jet size, quantity and placement. A Sweeper Jet
system combined with a properly sized and fully integrated
filtration system will assure cleaner water, reduced plugging and
fouling, and improved heat transfer efficiency. Suspended
particulate removal also optimizes chemical usage, saving
operational costs.
Specifications (pdf)
|
 |