Problem:
Effect of pressure change on scaling in pump and valve
- The solubility of CaCO3 decreases as pressure decreases.
At the tip of vane in a pump, the local pressure significantly drops
due to high rotating velocity (i.e., Bernoulli equation), resulting in
uncontrolled precipitation.
|
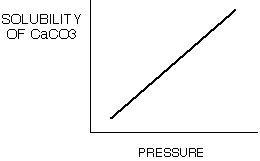 |
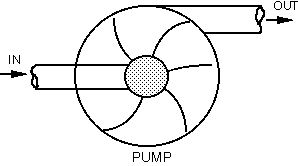 |
Solution:
- Electronic Descaling 2000 System
installed in inlet pipe
- Controlled Precipitation will Prevent
Impeller Fouling
|
Vertical Three Stage
Industrial Pump |
Problem:
A Peerless pump transporting quarry water used for service water
(cooling) and process water (slurry) in a cement plant fouled every 10 -
30 days and required an acid wash each time. The pump was mounted on a
floating platform located in the quarry. The pump had a 8" intake
pipe and a 12" output pipe transporting the water one half mile. The
CaCO3 of the quarry water was 400 ppm. The pump fouled every
ten days in the winter months and every thirty days during the summer
months. A crane was required at each of these shutdowns to remove and acid
wash the pump. The cost for this process was $1,000 per cleaning or
$24,000 per year.
|
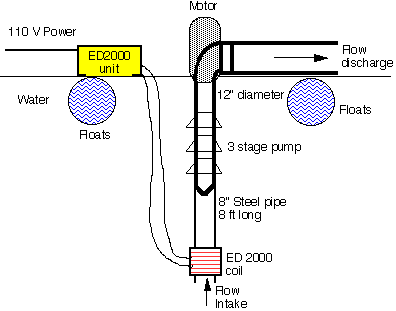 |
Solution:
The Electronic Descaling 2000 unit was installed on the pump intake.
Since the intake pipe was under water, a ceramic coated coil was used for
the protection from high pH water.
- The pump now operates continuously at
maximum efficiency (56 psi).
- The elimination of the acid wash has
significantly reduced maintenance costs.
- The expected life of the pump has been
extended.
|