Problem:
A plate and frame heat exchanger having
140 titanium plates with 14" feed (carbon steel) pipes was used to extract
heat from a 7 - 8% brine solution whose temperature ranged 90 - 100 degrees C
and hardness varied from 100 to 400 mg/L. The brine solution was cooled using a
fresh water which was pumped to the other side of the heat exchanger. Scaling
occurred in both sides of the heat exchanger, reducing the heat transfer
coefficient by 20% every two weeks. Scale build-up would force the plant to acid
clean the heat exchanger every 6 - 8 weeks. |
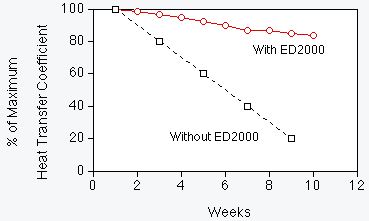 |
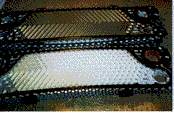 |
Solution:
Two Electronic Descaling 2000 units were installed: one on the brine inlet to
the plate and frame heat exchanger and the other on the fresh water inlet.
- The plate and frame heat exchanger now operates continuously at the almost
designed performance level. The overall heat transfer coefficient of 650
Btu/hr ft2 degrees F dropped only to 550 Btu/hr ft2 degrees F after 10 weeks
of operation.
- Downtime has been reduced almost to zero.
- Labor costs for maintenance has been drastically reduced.
- Chemicals and chemical disposal has been eliminated.
|
|
|
|